
Über RX Austria & Germany
RX Austria & Germany bewegt sich mitten in einem der spannendsten und größten Messemärkte und Wirtschaftsstandorte der Welt. Unser Portfolio wird geprägt von starken Marken aus den Bereichen Industrie, Gesundheit, Sport, Freizeit und Tourismus.
Ausgehend von unseren drei Standorten (Wien, Salzburg und Düsseldorf), bringt unser Team frische Ideen und neue Produkte in die Märkte und macht unsere Marken, Messen, Plattformen und Veranstaltungsorte zum „Place to be“ für unsere Communities – live, digital und an 365 Tagen im Jahr.
Zu RX Austria & Germany gehören RX Salzburg, RX Wien, RX Deutschland, Messe Wien Exhibition & Congress Center und STANDout.
Unsere Events
RX führt über 400 Veranstaltungen in 22 Ländern durch, persönlich und virtuell. In Österreich und Deutschland haben wir 22 Veranstaltungen im Portfolio. Unsere Veranstaltungen sind vielfältige, integrative, wirkungsvolle und kommerzielle Erlebnisse, bei denen Sie Ihr Geschäft aufbauen und erfolgreich sein können, egal wer und woher Sie sind.
Unsere nächsten Veranstaltungen
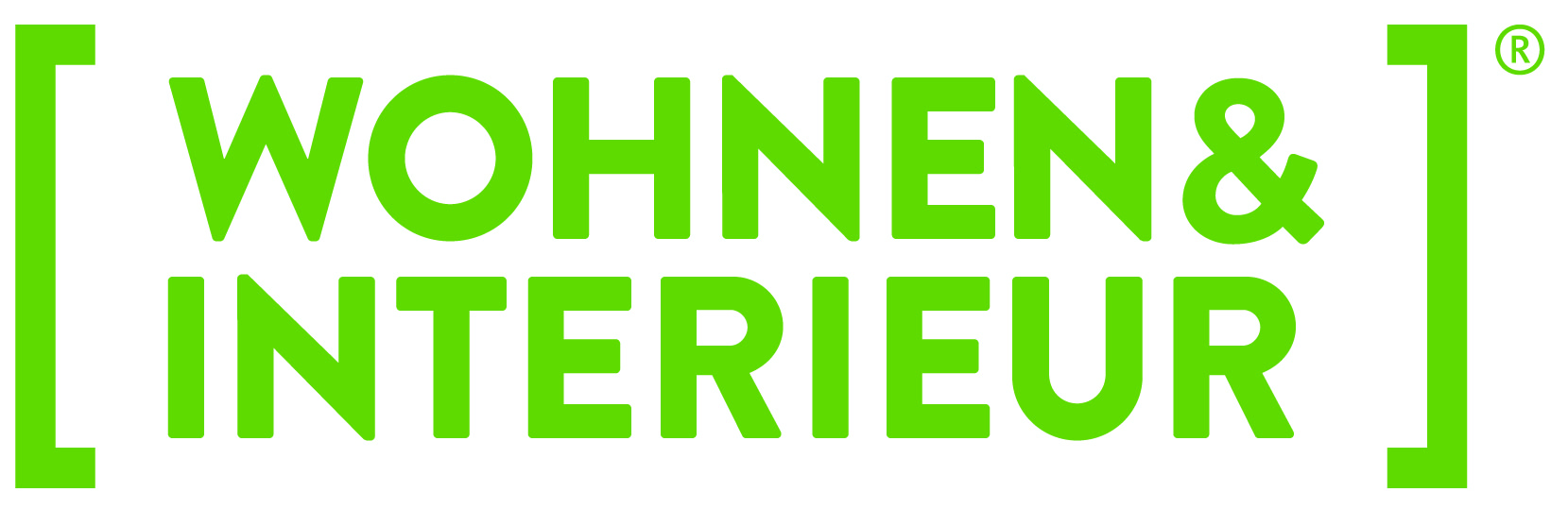
Hybrid
Wohnen & Interieur
Europe » Austria > Vienna
13th - 17th March 2024
Messe Wien Exhibition & Congress Center
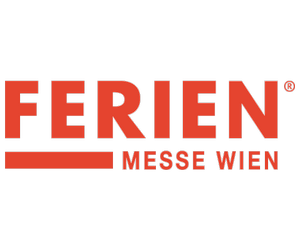
Hybrid
Ferien-Messe Wien
Europe » Austria > Vienna
14th - 17th March 2024
Messe Wien Exhibition & Congress Center
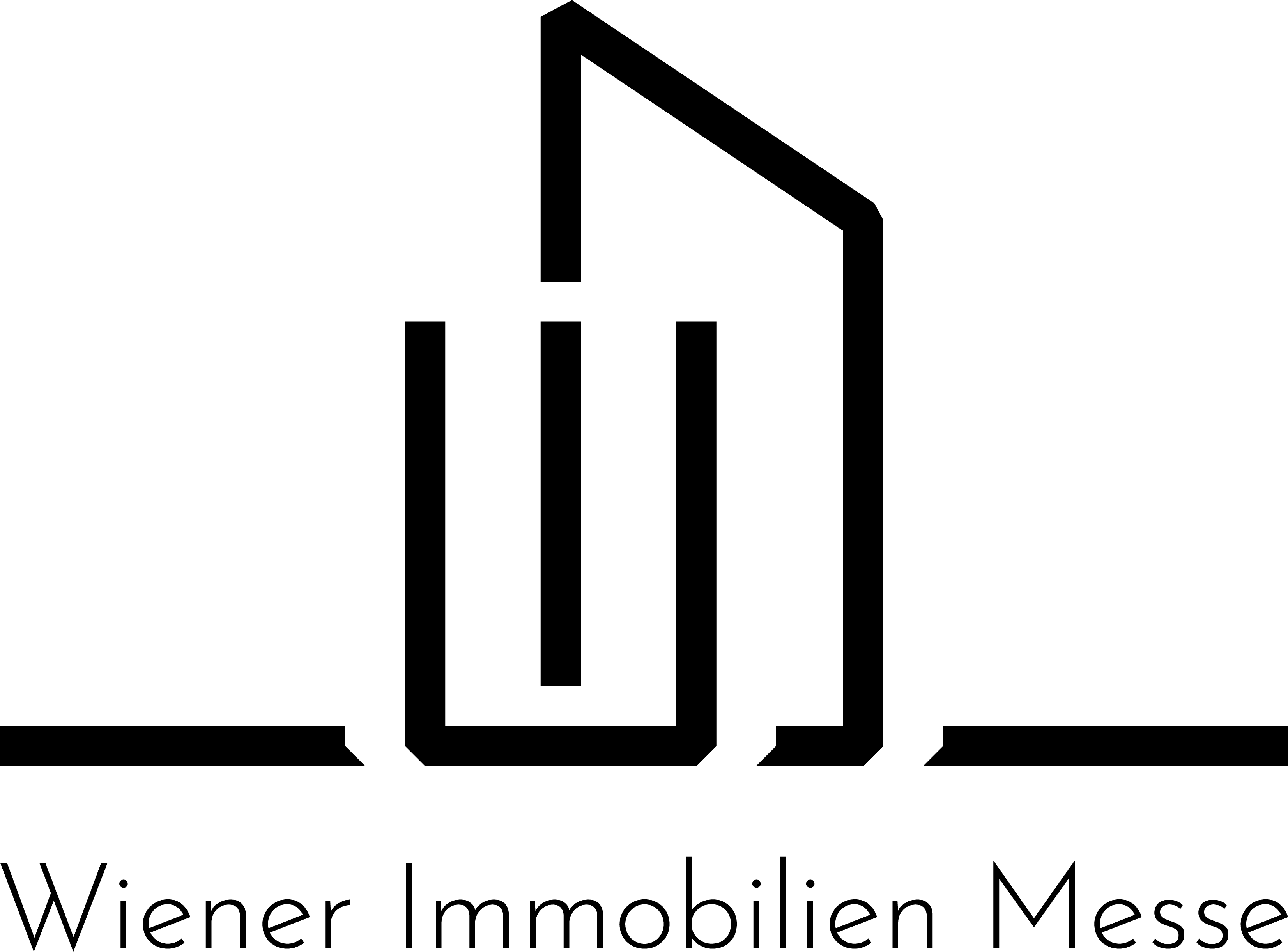
Hybrid
Wiener Immobilienmesse
Europe » Austria > Vienna
16th - 17th March 2024
Messe Wien Exhibition & Congress Center
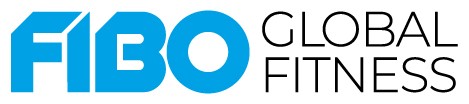
Hybrid
FIBO
Europe » Germany > Cologne
11th - 14th April 2024
Exhibition Centre Cologne
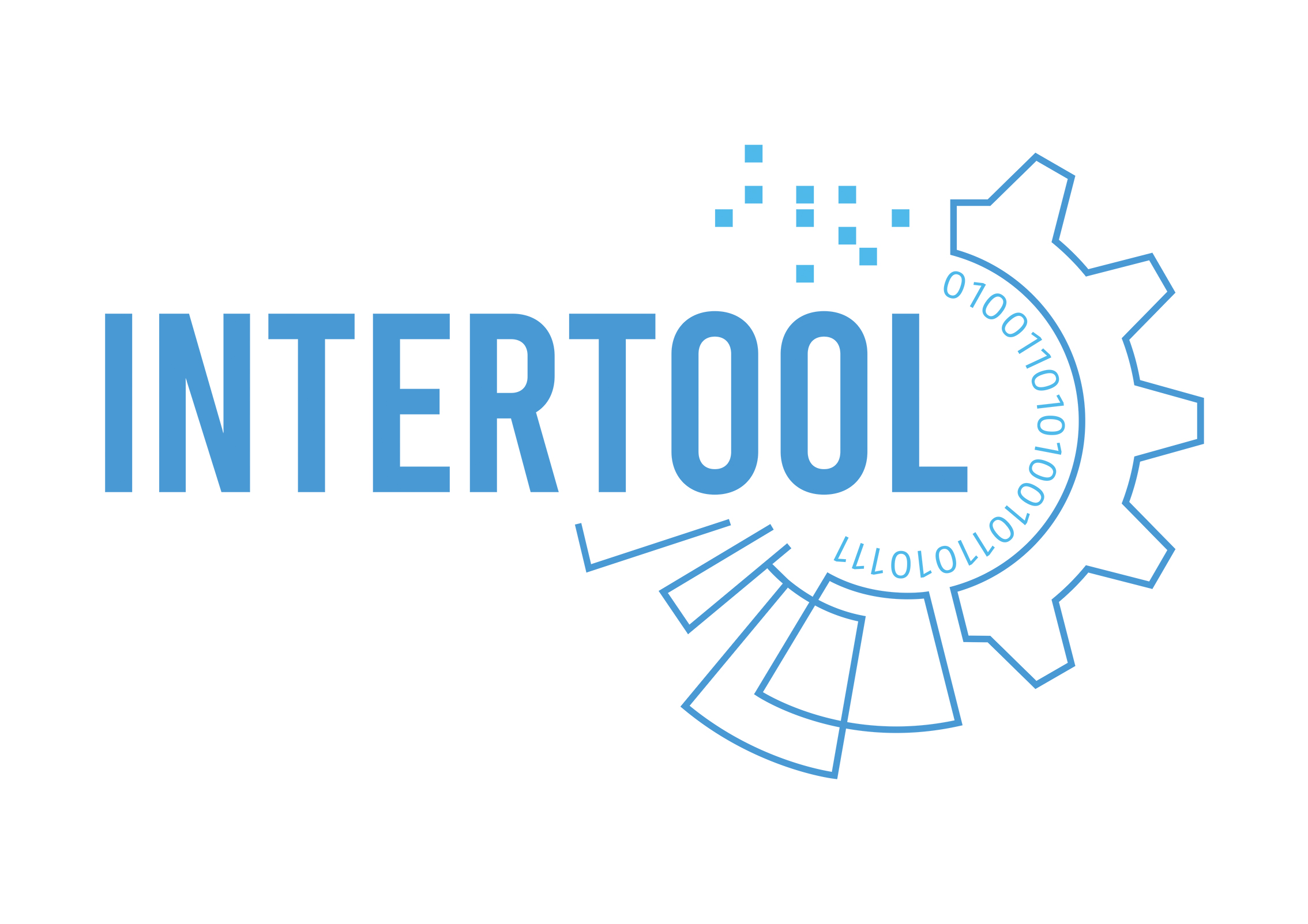
Hybrid
INTERTOOL
Europe » Austria > Wels
23rd - 26th April 2024
Messe Wels
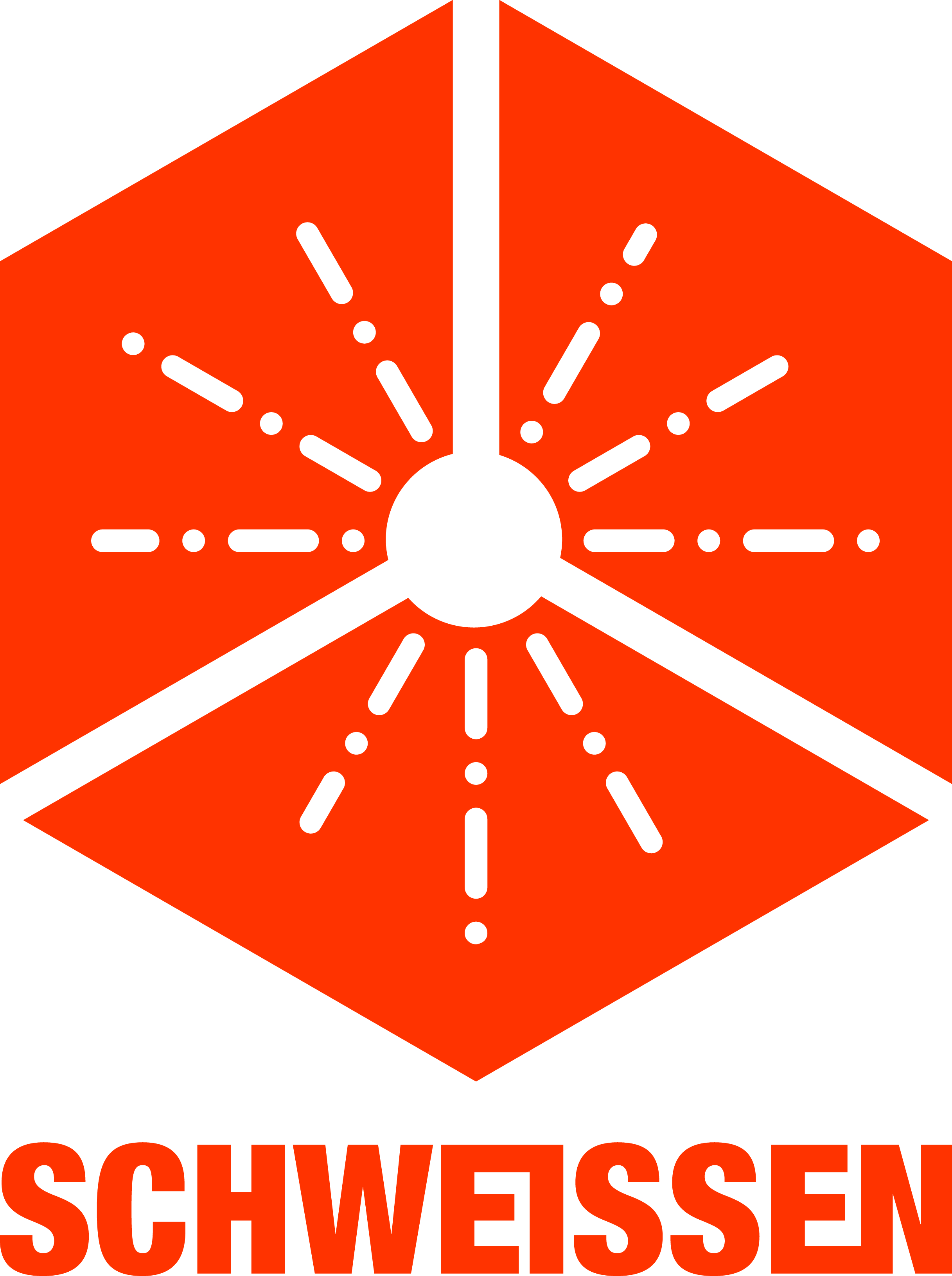
Hybrid
SCHWEISSEN
Europe » Austria > Wels
23rd - 26th April 2024
Messe Wels
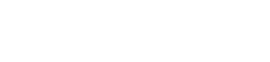
Hybrid
Elektrofachhandelstage
Europe » Austria > Linz
27th - 28th September 2024
Design Center Linz
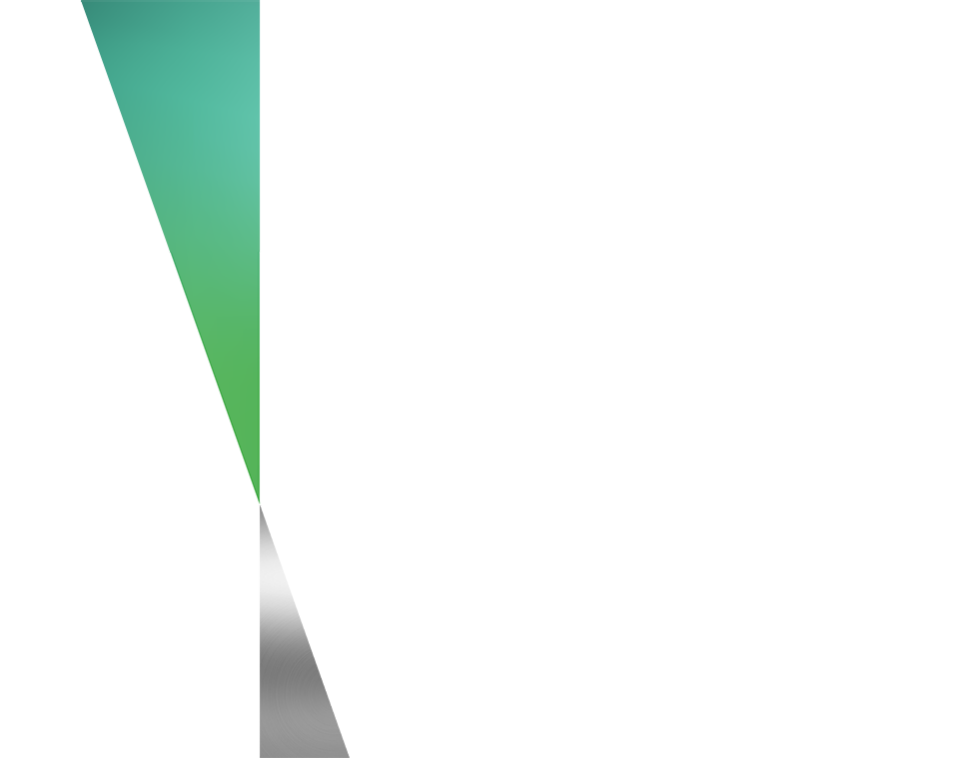
Hybrid
ALUMINIUM
Europe » Germany > Dusseldorf
8th - 10th October 2024
Dusseldorf Exhibition Centre
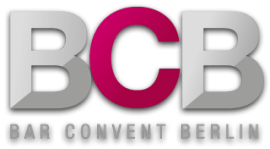
Hybrid
Bar Convent Berlin
Europe » Germany > Berlin
14th - 16th October 2024
Exhibition Centre Berlin
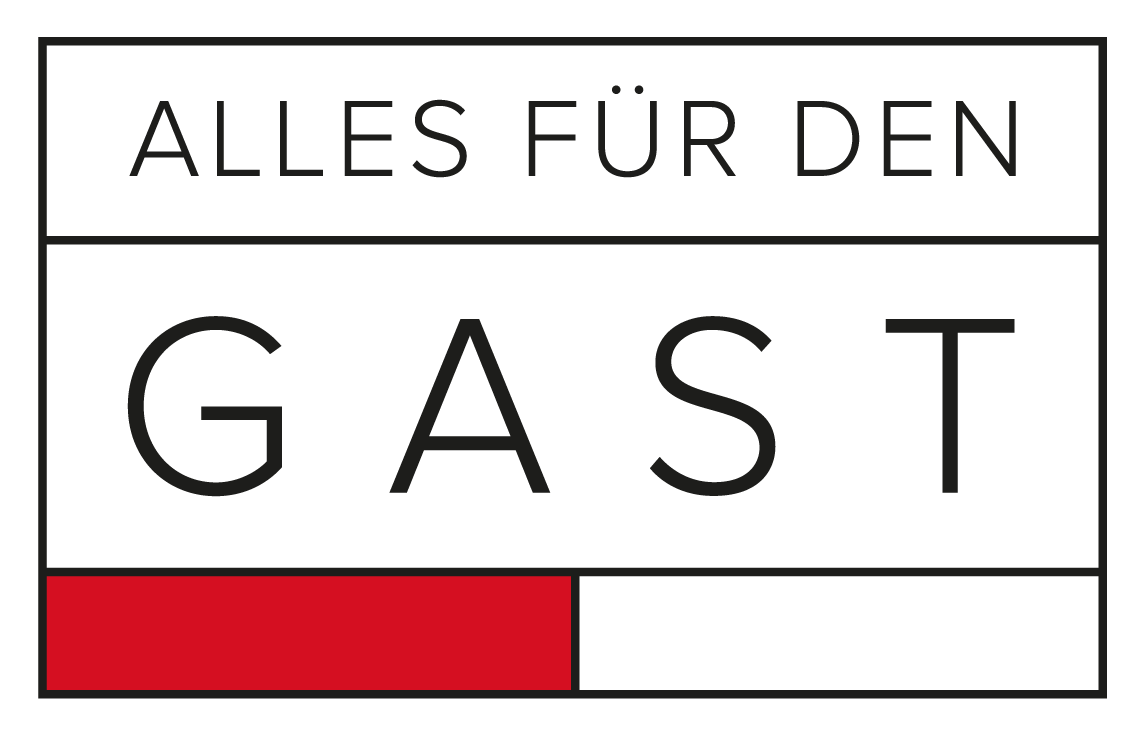
Hybrid
Alles fur den Gast
Europe » Austria > Salzburg
9th - 13th November 2024
Messezentrum Salzburg
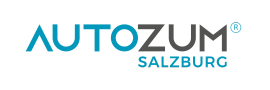
Hybrid
AutoZum
Europe » Austria > Salzburg
21st - 24th January 2025
Messezentrum Salzburg
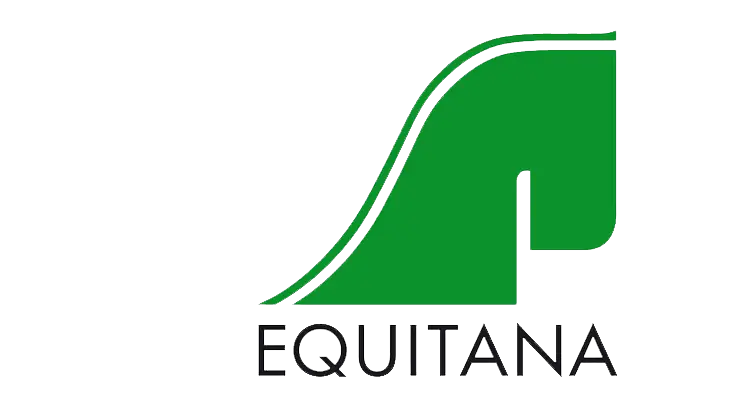
Hybrid
EQUITANA
Europe » Germany > Essen
6th - 12th March 2025
Messegelände Essen

Hybrid
Austropharm
Europe » Austria > Vienna
24th - 26th April 2025
Messe Wien Exhibition & Congress Center
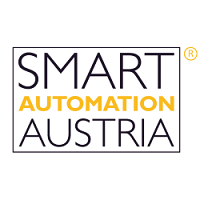
Hybrid
Smart Automation Austria
Europe » Austria > Linz
20th - 22nd May 2025
Design Center Linz
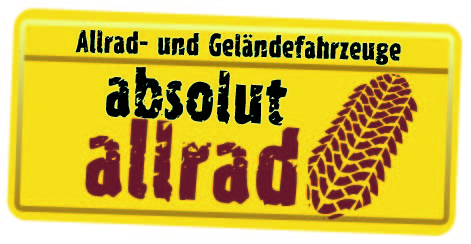
Hybrid
Absolut Allrad
Europe » Austria > Salzburg
TBC
Messezentrum Salzburg
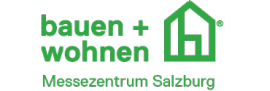
Hybrid
Bauen & Wohnen Salzburg
Europe » Austria > Salzburg
TBC
Messezentrum Salzburg
_Logo_RGB_72dpi.png)
Hybrid
Power-Days
Europe » Austria > Salzburg
TBC
Messezentrum Salzburg
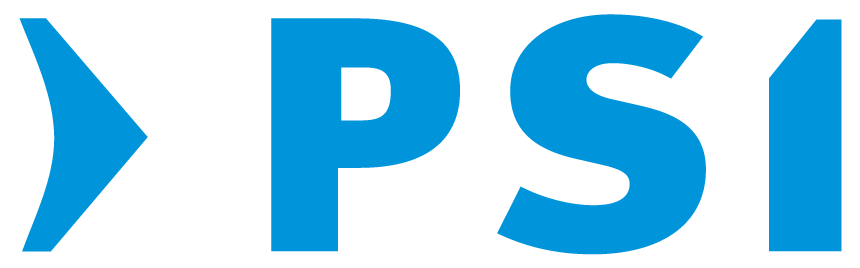
Hybrid
PSI Trade Show
Europe » Germany > Dusseldorf
TBC
Dusseldorf Exhibition Centre
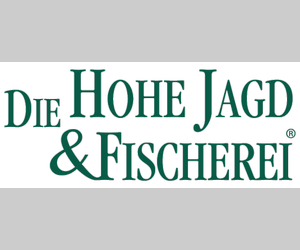
Hybrid
Hohe Jagd & Fischerei
Europe » Austria > Salzburg
TBC
Messezentrum Salzburg
Wir sind RX
My goal is to create a work environment that helps everybody to find a fulfilling purpose, have fun, be pushed, be accountable and succeed. A place where people feel safe to truly express themselves and have the courage to make the big bets, but also to acknowledge and learn from bets that falter and not be discouraged to try again.




